Finishing your product fast and precisely
Direct Female Tools
In recent years, the series production of structural parts for wind turbines has been a complex three-step process. Negative moulds were taken from the master model and the components were finished in them, with the master mould often still being built manually. It sometimes took several years from the computer-calculated blade mould to series production. Knierim's Direct Female Tooling (DFT), in which a hundred or more individual moulds can be produced without any loss of quality, streamlines the production process considerably.
The basic structure of the positive core and DFT is the same: a steel substructure is calculated and built from the customer's 3D geometry, to which milled mall frames are screwed in the small, 6x5x2 m five-axis machine. Plywood panels are attached to crossbars and covered with a laminate. The specialists glue balsa wood to this as the core of a sandwich construction, which is roughed into shape using one of the two "CMS Poseidon" 5-axis milling machines measuring up to 34 x 8.50 x 4 meters. This is followed by the inner layer of laminate, which is made of GRP in the original form (like the outer layer) and is then epoxy-pasted, roughed and finished by a milling machine.
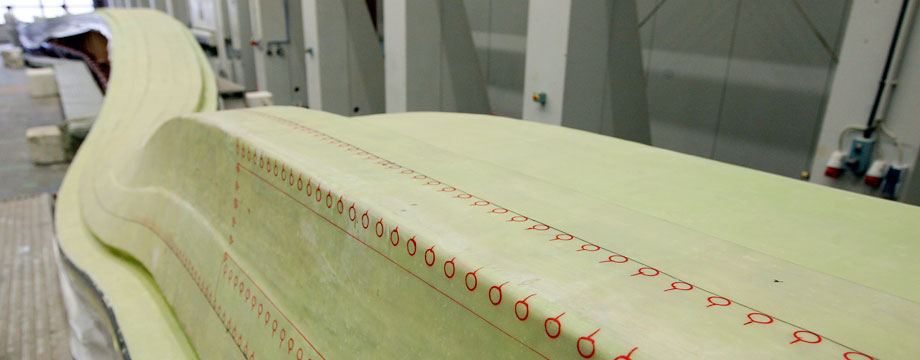
In the direct negative mould, the top and bottom layers of the sandwich construction are laminated and milled directly from GRP or CFRP - i.e. glass fibre reinforced or carbon fibre reinforced plastic - depending on the subsequent requirements for the components. In the high-end sector, a heating layer is applied first. This can either be a wire mesh or a carbon fibre blanket from the Bremen-based company fibretech (only possible on CfK laminate). Both are later connected to electricity in the low-voltage range (48 to 60 volts) and generate an evenly distributed, surface-covering heat due to the resistance of the supporting top layer. This tempering process optimises the curing of the components in the final production stage.
The heating layer is then coated with an excess of laminate before roughing and finishing takes place. Here too, an end mill is used in the edge areas and a radial copy milling cutter (ball end mill) is used on the surface. Roughing is performed by a solid carbide milling cutter and finishing by an indexable insert milling cutter with up to 400 revolutions per minute. The milling head of the machines runs in length and width at a feed rate of up to 85 meters per minute and 45 m/min in height. The rotations in the B-axis (110 degrees) and C-axis (300 degrees) ensure an optimum approach angle of the milling cutter at every point on the model.
Finishing the process involves spraying on a top coat resin (primer), which is sanded and polished by experienced Knierim boat builders. Dimensional markings can be applied at the very end.
"Customer experience shows that DFT is the mould construction of the future for most structural parts," explains Managing Director Steffen Müller, "we are continuing to develop the technology and also adapting it to the specific needs of our customers."